1. 目的
本规范适用于家电类电子产品的PCB 工艺设计,运用于但不限于PCB 的设计、PCB 批产工艺审查、单板工艺审查等活动。 本规范之前的相关标准、规范的内容如与本规范的规定相抵触的,以本规范为准 3.引用/参考标准或资料 TS—S0902010001 <<信息技术设备PCB 安规设计规范>> TS—SOE0199001 <<电子设备的强迫风冷热设计规范>> TS—SOE0199002 <<电子设备的自然冷却热设计规范>> IEC60194 <<印制板设计、制造与组装术语与定义>> (Printed Circuit Board design manufacture and assembly-terms and definitions) IPC—A—600F <<印制板的验收条件>> (Acceptably of printed board) IEC60950 4.规范内容
4.1焊盘的定义
1) 孔径尺寸: |
Part | Z(mm) | G(mm) | X(mm) | Y(ref) | |
Chip Resistors and Capacitors | 0201 | 0.76 | 0.24 | 0.30 | 0.26 |
0402 | 1.45~1.5 | 0.35~0.4 | 0.55 | 0.55 | |
C0603 | 2.32 | 0.72 | 0.8 | 1.8 | |
R0603 | 2.4 | 0.6 | 1.0 | 0.9 | |
L0603 | 2.32 | 0.72 | 0.8 | 0.8 | |
C0805 | 2.85 | 0.75 | 1.4 | 1.05 | |
R0805 | 3.1 | 0.9 | 1.6 | 1.1 | |
L0805 | 3.25 | 0.75 | 1.5 | 1.25 | |
1206 | 4.4 | 1.2 | 1.8 | 1.6 | |
1210 | 4.4 | 1.2 | 2.7 | 1.6 | |
1812 | 5.8 | 2.0 | 3.4 | 1.9 | |
1825 | 5.8 | 2.0 | 6.8 | 1.9 | |
2010 | 6.2 | 2.6 | 2.7 | 1.8 | |
2512 | 7.4 | 3.8 | 3.2 | 1.8 | |
3216(Type A) | 4.8 | 0.8 | 1.2 | 2.0 | |
Tantalum Capacitors | 3528(Type B) | 5.0 | 1.0 | 2.2 | 2.0 |
6032(Type C) | 7.6 | 2.4 | 2.2 | 2.6 | |
7343(Type D) | 9.0 | 3.8 | 2.4 | 2.6 | |
2012(0805) | 3.2 | 0.6 | 1.6 | 1.3 | |
3216(1206) | 4.4 | 1.2 | 2.0 | 1.6 | |
3516(1406) | 4.8 | 2.0 | 1.8 | 1.4 | |
5923(2309) | 7.2 | 4.2 | 2.6 | 1.5 | |
2012Chip(0805) | 3.0 | 1.0 | 1.0 | 1.0 | |
Inductors | 3216 Chip(1206) | 4.2 | 1.8 | 1.6 | 1.2 |
4516 Chip(1806) | 5.8 | 2.6 | 1.0 | 1.6 | |
2825Prec(1110) | 3.8 | 1.0 | 2.4 | 1.4 | |
3225Prec(1210) | 4.6 | 1.0 | 2.0 | 1.8 | |
对于SOP、QFP焊盘的设计标准。(如下图表所示)
焊盘大小要根据元器件的尺寸确定,焊盘的宽度=引脚宽度+2*引脚高度,焊接效果最好;焊盘的长度见图示L2,(L2=L+b1+b2;b1=b2=0.3mm+h;h=元件脚高)
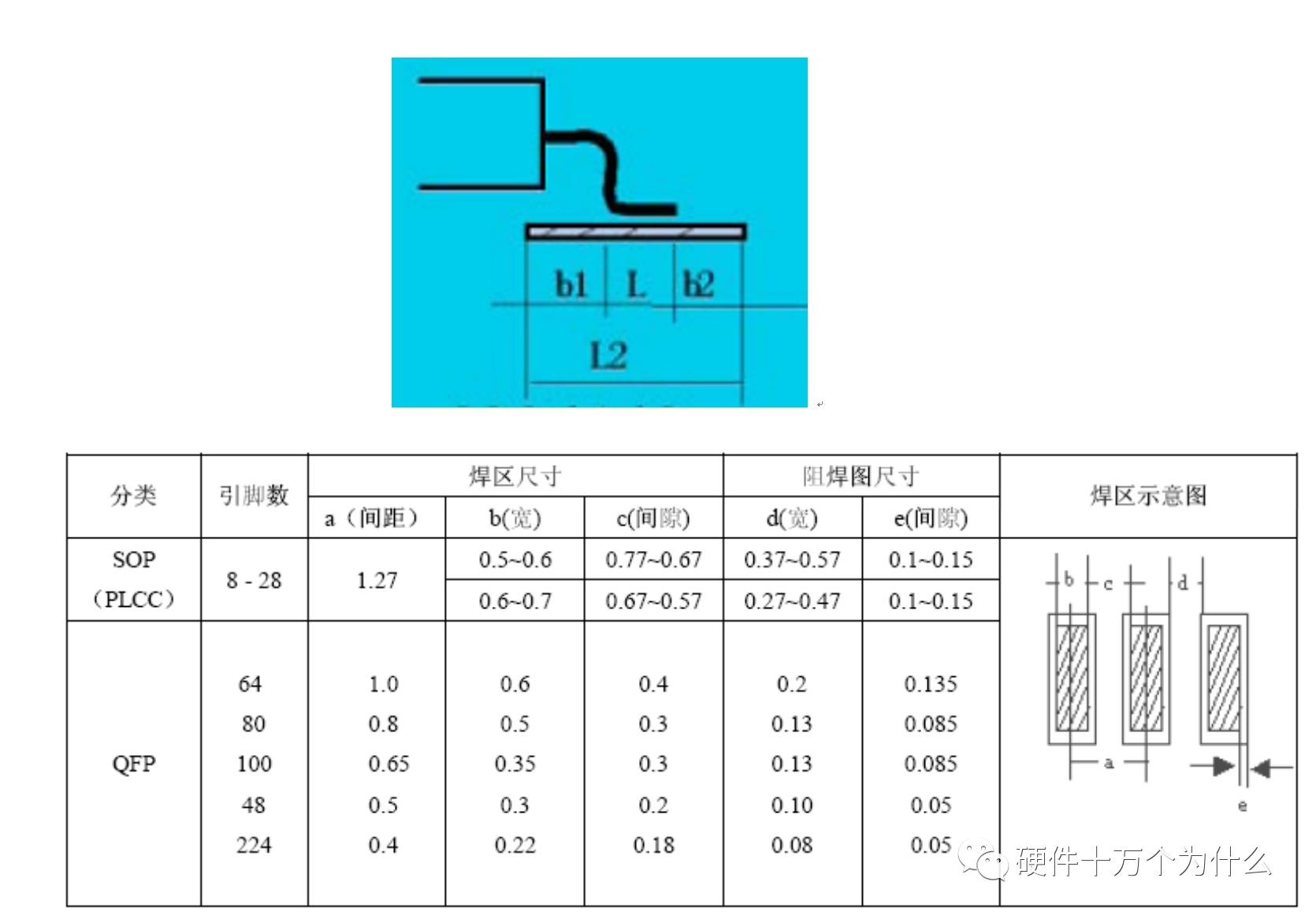
4.4.4.4未做特别要求时,通孔安装元件焊盘的规格如下:
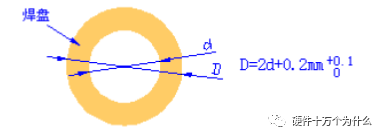
4.4.4.5针对引脚间距≤2.0mm的手插PIN、电容等,焊盘的规格为:①多层板焊盘直径=孔径+0.2~0.4mm;②单层板焊盘直径=2×孔径
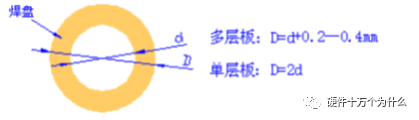
4.4.4.6 常见贴片IC焊盘设计,详见附件(下图只是一个选图,相关尺寸见附件)
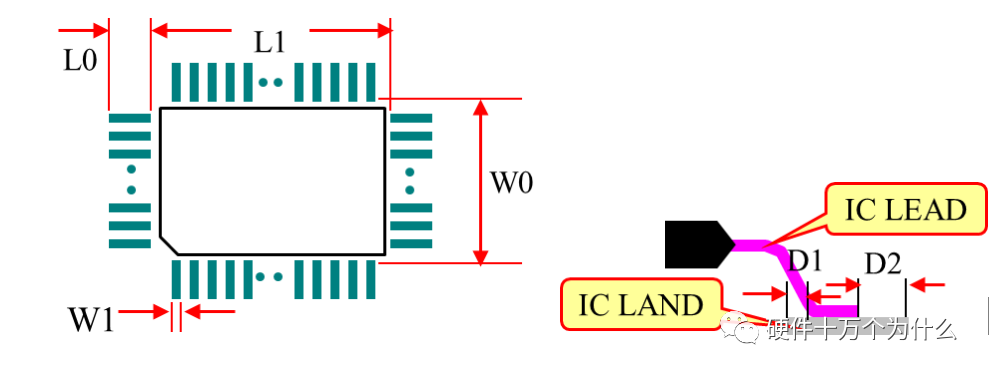
4.4.5 新器件的PCB 元件封装库应确定无误
4.4.5.1 PCB 上尚无件封装库的器件,应根据器件资料建立新的元件封装库,并保证丝印库存与实物相符合,特别是新建立的电磁元件、自制结构件等的元件库是否与元件的资料(承认书、规格书、图纸)相符合。新器件应建立能够满足不同工艺(回流焊、波峰焊、通孔回流焊)要求的
元件库。
4.4.5.2 需过波峰焊的SMT 器件要求使用表面贴波峰焊盘库
4.4.5.3 轴向器件和跳线的引脚间距的种类应尽量少,以减少器件的成型和安装工具。
4.4.5.4 不同PIN 间距的兼容器件要有单独的焊盘孔,特别是封装兼容的继电器的各兼容焊盘之间要连线。
4.4.5.5 不能用表贴器件作为手工焊的调测器件,表贴器件在手工焊接时容易受热冲击损坏。
4.4.5.6 除非实验验证没有问题,否则不能选用和PCB 热膨胀系数差别太大的无引脚表贴器件,
这容易引起焊盘拉脱现象。
4.4.5.7 除非实验验证没有问题,否则不能选非表贴器件作为表贴器件使用。因为这样可能需要手焊接,效率和可靠性都会很低。
4.4.5.8 多层PCB 侧面局部镀铜作为用于焊接的引脚时,必须保证每层均有铜箔相连,以增加镀铜的附着强度,同时要有实验验证没有问题,否则双面板不能采用侧面镀铜作为焊接引脚。
4.4.6 需波峰焊加工的单板背面器件不形成阴影效应的安全距离,考虑波峰焊工艺的SMT器件距离要求如下:
1) 相同类型器件距离(如图)
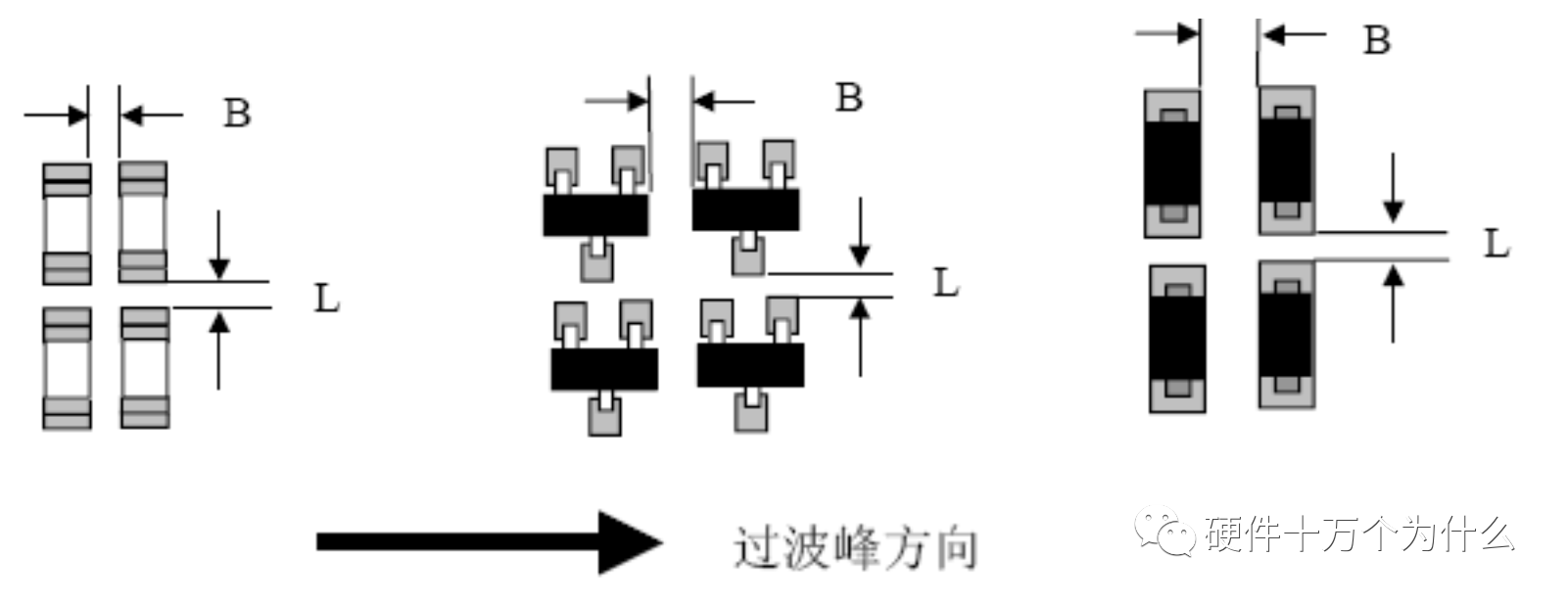
相同类型器件的封装尺寸与距离关系:
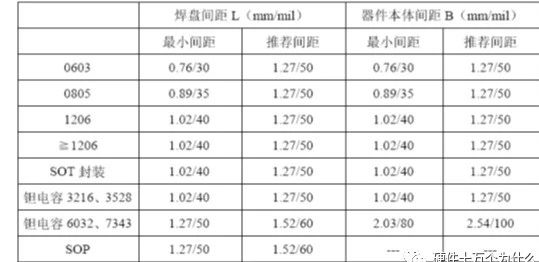
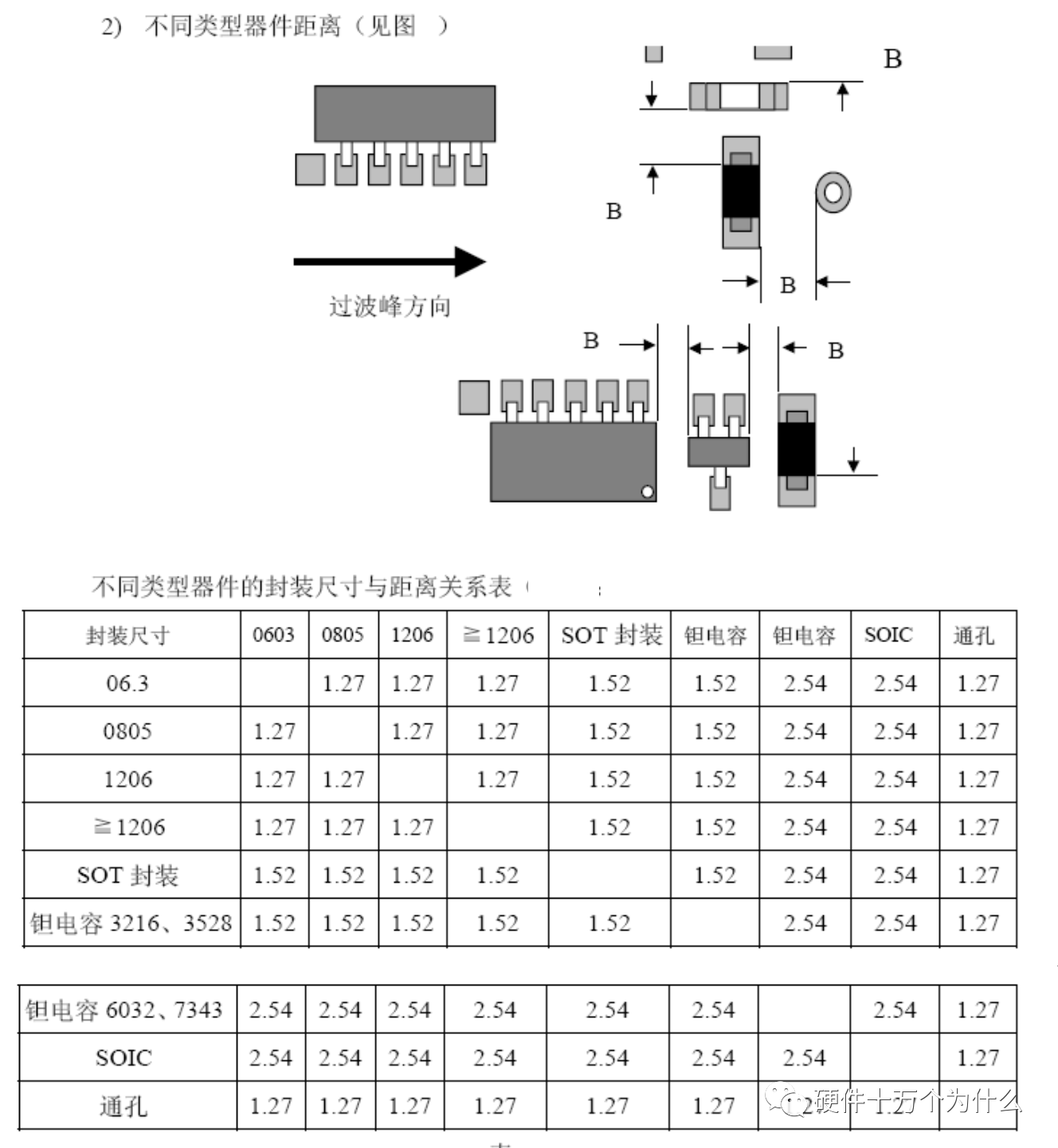
1. 4.6.1 SMD同种元件间隔应满足≥0.3mm,异种元件间隔≥0.13*h+0.3mm(注:h指两种不同零件的高度差),THT元件间隔应利于操作和替换
2. 4.6.2 贴装元件焊盘的外侧与相邻插装元件的外侧距离大于2mm
3. 4.6.3经常插拔器件或板边连接器周围3mm 范围内尽量不布置SMD(尤其是BGA),以防止连接器插拔时产生的应力损坏器件;
4. 4.6.4 定位孔中心到表贴器件边缘的距离不小于5.0mm
5. 4.6.5 大于0805 封装的陶瓷电容,布局时尽量靠近传送边或受应力较小区域,其轴向尽量与
进板方向平行,尽量不使用1825 以上尺寸的陶瓷电容。(保留意见
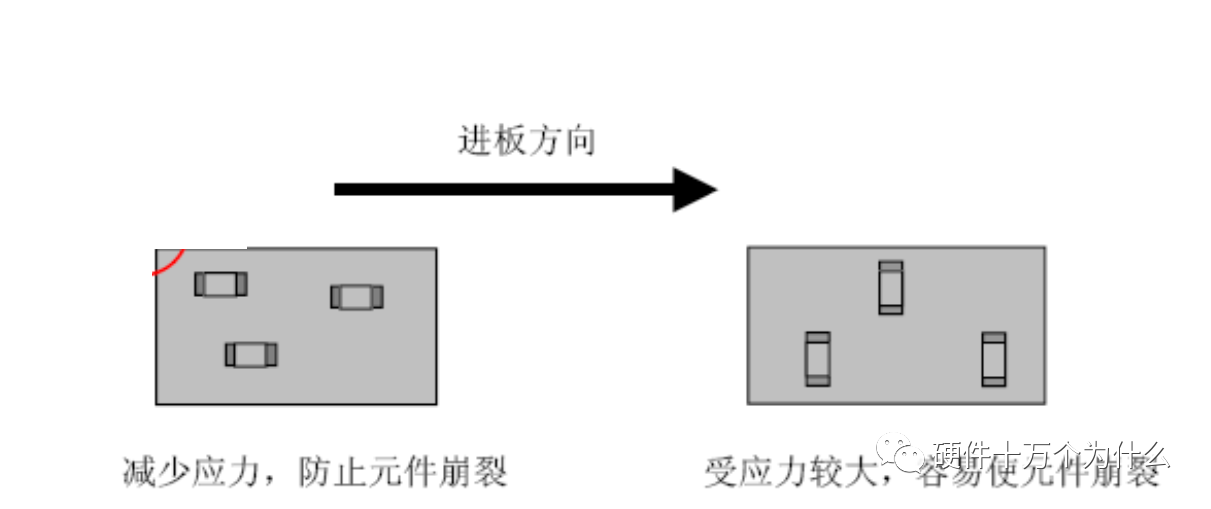
4.4.6.6 经常插拔器件或板边连接器周围3mm 范围内尽量不布置SMD,以防止连接器插拔时产生的应力损坏器件。如图:
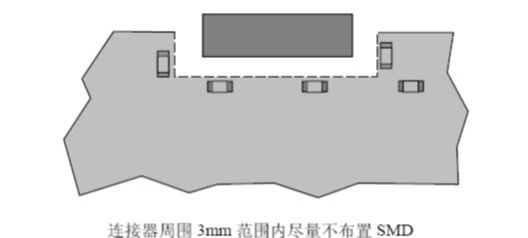
4.4.6.7 过波峰焊的表面贴器件的stand off 符合规范要求过波峰焊的表面贴器件的stand off 应小于0.15mm,否则不能布在B 面过波峰焊,若器件的stand off 在0.15mm 与0.2mm 之间,可在器件本体底下布铜箔以减少器件本体底部与PCB表面的距离。
4.4.6.8 波峰焊时背面测试点不连锡的最小安全距离已确定
为保证过波峰焊时不连锡,背面测试点边缘之间距离应大于1.0mm。
4.4.6.9 过波峰焊的插件元件焊盘间距大于1.0mm
为保证过波峰焊时不连锡,过波峰焊的插件元件焊盘边缘间距应大于1.0mm(包括元件本身引脚的焊盘边缘间距)。优选插件元件引脚间距(pitch)≧2.0mm,焊盘边缘间距≧1.0mm。在器件本体不相互干涉的前提下,相邻器件焊盘边缘间距满足图要求
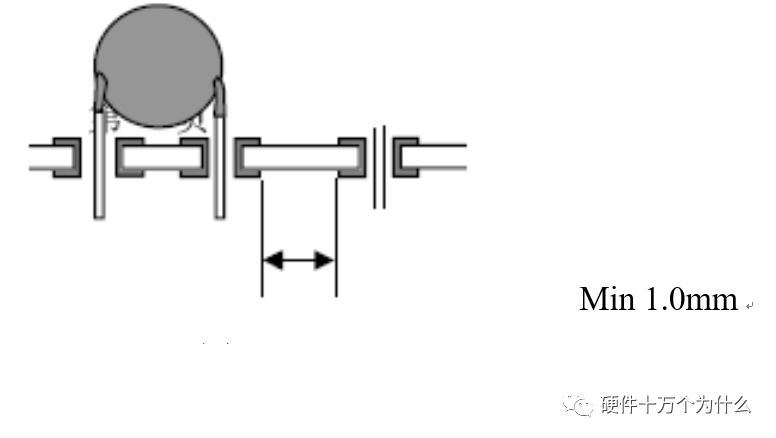
4.4.6.10 插件元件每排引脚为较多,以焊盘排列方向平行于进板方向布置器件时,当相邻焊盘边缘间距为0.6mm--1.0mm 时,推荐采用椭圆形焊盘或加偷锡焊盘
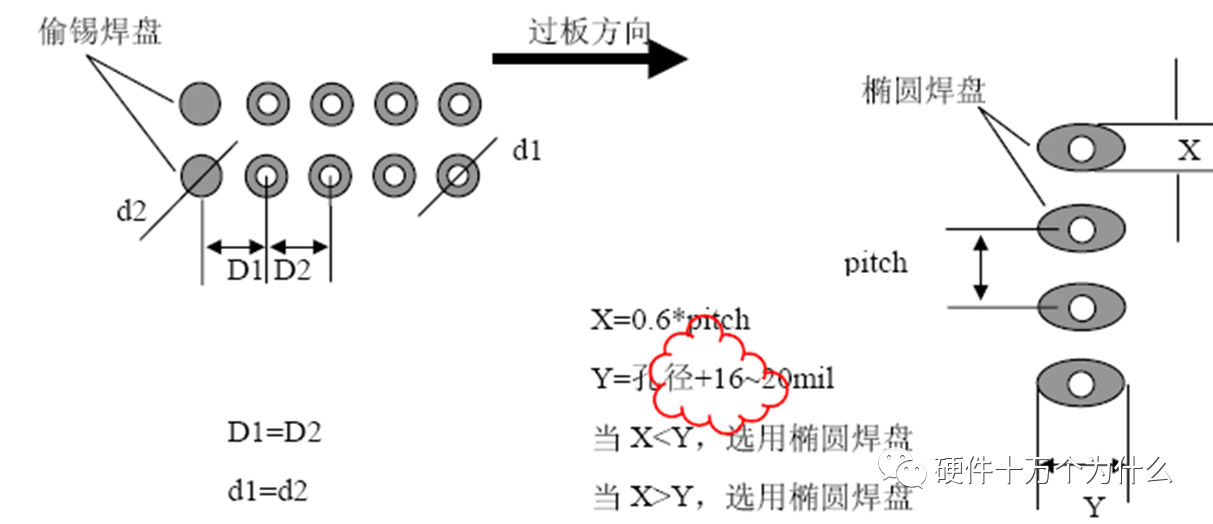
4.4.6.11 贴片元件之间的最小间距满足要求
机器贴片之间器件距离要求(如图):
同种器件:≧0.3mm
异种器件:≧0.13*h+0.3mm(h 为周围近邻元件最大高度差)
手工贴片的元件之间距离要求:≧1.5mm。
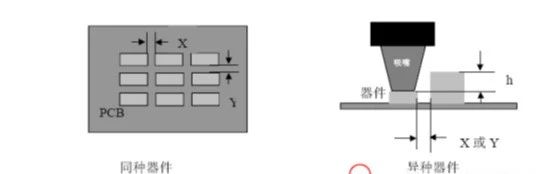
4.4.6.12 元器件的外侧距过板轨道接触的两个板边大于、等于5mm(图9)
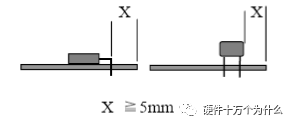
为了保证制成板过波峰焊或回流焊时,传送轨道的卡爪不碰到元件,元器件的外侧距板边距离应大于或等于5mm,若达不到要求,则PCB 应加工艺边,器件与V—CUT 的距离≧1mm
4.4.6.13 可调器件、可插拔器件周围留有足够的空间供调试和维修应根据系统或模块的PCBA安装布局以及可调器件的调测方式来综合考虑可调器件的排布方向、调测空间;可插拔器件周围空间预留应根据邻近器件的高度决定。
4.4.6.14 所有的插装磁性元件一定要有坚固的底座,禁止使用无底座插装电感
4.4.6.15 有极性的变压器的引脚尽量不要设计成对称形式;有空脚不接电路时,注意加上焊盘,以增加焊接牢固性
4.4.6.16 安装孔的禁布区内无元器件和走线(不包括安装孔自身的走线和铜箔)
4.4.6.17 金属壳体器件和金属件与其它器件的距离满足安规要求
金属壳体器件和金属件的排布应在空间上保证与其它器件的距离满足安规要求。
4.4.6.18 对于采用通孔回流焊器件布局的要求
a. 对于非传送边尺寸大于300mm 的PCB,较重的器件尽量不要布置在PCB 的中间,
以减轻由于插装器件的重量在焊接过程对PCB 变形的影响,以及插装过程对板上已
经贴放的器件的影响。
b. 为方便插装,器件推荐布置在靠近插装操作侧的位置。
c. 尺寸较长的器件(如内存条插座等)长度方向推荐与传送方向一致。多个引脚在同一直线上的器件,连接器、DIP 封装器件、T220 封装器件,布局时应使其轴线和波峰焊方向平行。
较轻的器件如二级管和1/4W 电阻等,布局时应使其轴线和波峰焊方向垂直。这样能防止过波峰焊时因一端先焊接凝固而使器件产生浮高现象;直插元件应避免使用方形焊盘(方形焊盘容易导致上锡不良和连焊)
5.相关管理内容
5.1 元件焊盘的封装库5.2 PCB焊盘设计的工艺性在遵守上面规则的前提下,需要具体的变化以实际设计需要为准。